Så tillverkade Sandvik världens första 3D-printade, krocksäkra gitarr
Rockstjärnor har slagit sönder gitarrer i årtionden, men få har gjort det med större entusiasm än den svenskfödde gitarrvirtuosen Yngwie Malmsteen. Sandvik bestämde sig för att testa sin spjutspetsteknik genom att bygga världens första okrossbara gitarr helt i metall och låta Malmsteen släppa loss sina slagfärdigheter på den.
Titta på filmen som visar hur gitarren skapades:
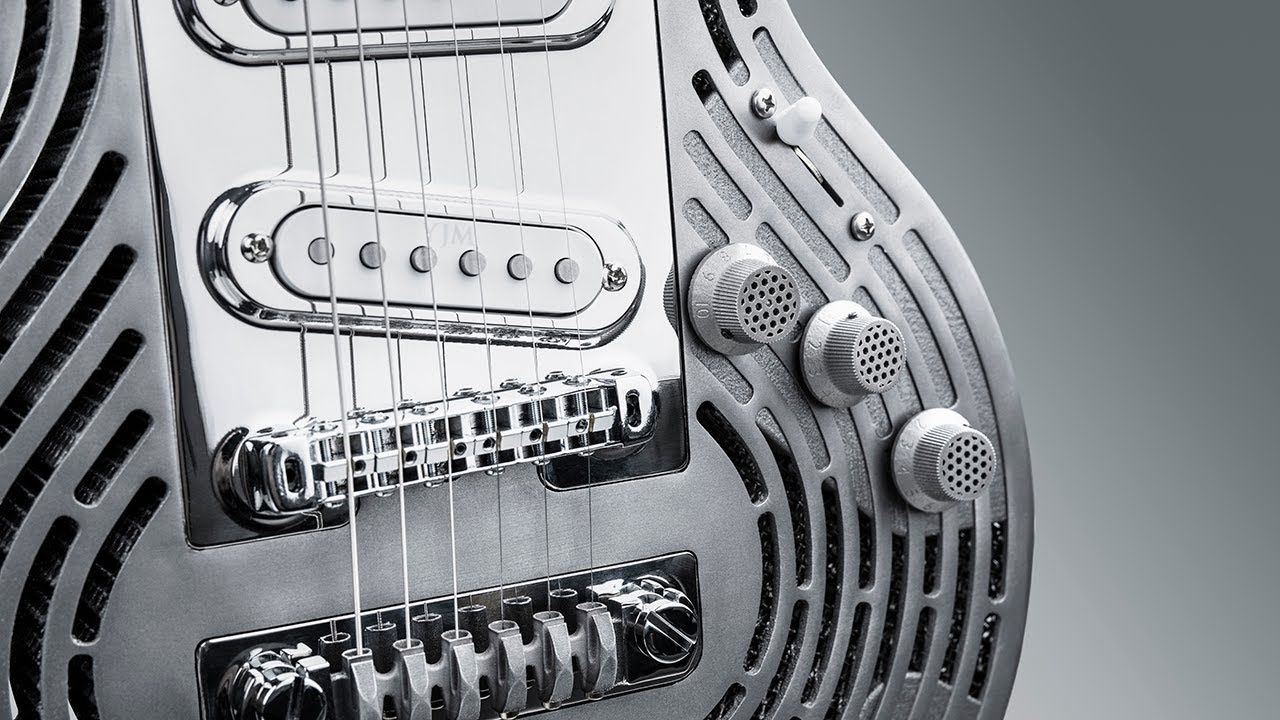
I det här projektet samlade Sandvik experter från hela företaget för att visa hur de kunde använda hållbara, banbrytande tekniker för att tillverka något som är både mycket exakt och otroligt hållbart.
Världens första smällsäkra gitarr
Henrik Loikkanen, processutvecklare inom maskinbearbetning på Sandvik Coromant, har spelat gitarr sedan han var ung och beundrade Malmsteen. För att förstå vad som händer när Malmsteen förstör ett instrument vände sig Loikkanen till YouTube.
"Vi var tvungna att konstruera en gitarr som inte går att slå sönder på alla de olika sätt som man kan slå sönder en gitarr på", säger Loikkanen. "Den tekniska utmaningen var den kritiska skarven mellan halsen och kroppen som vanligtvis spricker på en gitarr."
Sandviks ingenjörer eliminerade skarven mellan hals och kropp. I stället frästes gitarrens hals och greppbräda i en och samma maskin från massiva stänger av återvunnet rostfritt stål, en gitarrkonstruktion som aldrig tidigare hade prövats. Både halsen och greppbrädan förlängdes in i ett rektangulärt "nav" som skulle nå djupt in i gitarrens kropp.
Yngwie Malmsteen discussing design details of the guitar neck and hub with members of the Sandvik team.
Data i framkant
Långa, smala komponenter som greppbrädan och halsen är särskilt känsliga för distorsion. Med hjälp av avancerad programvara kunde Sandvik Coromant simulera fräsningen digitalt innan den första skärningen gjordes, vilket möjliggjorde rätt val av verktyg, sparade tillverkningstid och säkerställde effektiva processer.
"Precisionen var avgörande", säger Henrik Loikkanen, utvecklare av bearbetningsprocesser på Sandvik Coromant. "Vår programvara bygger på många års erfarenhet och ger rekommendationer om verktyg och skärdata som hjälpte oss att fräsa ner greppbrädan till en utmanande tjocklek på 1 millimeter på vissa ställen."
Inspection of the ILS (Isotropic Lightweight Structure), an integral component of the guitar. The ILS is made from Sandvik hyper-duplex stainless steel.
En 3D-printad titankropp i lager
Samtidigt tog man sig an en annan utmaning - hur man skulle tillverka gitarrkroppen, en extremt komplex design på grund av behovet av hög hållfasthet vid låg vikt.
Sandvik, som förlitar sig på sin världsledande expertis inom metallpulver och additiv tillverkning, bestämde sig för att 3D-printa kroppen. Lasrar ritade upp en design i bäddar av fint titanpulver och smälte samman lager av material ovanpå varandra. Skikten, som vart och ett var tunnare än ett hårstrå, byggdes upp till gitarrens kropp.
"Med additiv tillverkning kan vi skapa lättare, starkare och mer flexibla komponenter med interna strukturer som skulle vara omöjliga att fräsa på traditionellt sätt", säger Amelie Norrby, ingenjör inom additiv tillverkning som deltog i gitarrprojektet. "Och det är mer hållbart eftersom man bara använder det material som behövs för komponenten, vilket minimerar avfallet."
Den här gitarren är en riktig best! Sandvik är uppenbarligen på toppen av sitt spel.
"The most important thing for me is the neck," says Yngwie Malmsteen, here checking the straightness.
Materialens värld
Tomas Forsman, specialist inom forskning och utveckling på Sandvik, insåg att gitarren behövde en speciell struktur som var stark, styv och lätt. Han föreslog en isotropisk lättviktsstruktur (ILS), den starkaste strukturen för en given vikt som någonsin uppfunnits.
"Den ser ut ungefär som vilken ramstruktur som helst", säger Forsman, "men den är faktiskt styvare och lättare än något vi sett tidigare."
Forsman visste också exakt vilket material ILS:en skulle tillverkas av: hyperduplexstål, en stålsort som endast Sandvik tillverkar. Han ville placera hyper-duplex ILS mellan gitarrens hals och greppbräda.
Att samarbeta på det här sättet är en nyckel för framtiden
Men greppbrädan fick inte vridas, vilket är ett problem när man svetsar ihop långa, tunna komponenter. Genom analys och testning finjusterades svetsprocessen tills ILS kunde integreras på ett framgångsrikt sätt.
Forsman anser att gitarrprojektet och det samarbete som krävdes illustrerar hur Sandviks djupa expertis och erfarenhet kan lösa unika utmaningar, även med korta tidsramar.
"Att samarbeta på det här sättet är en nyckel för framtiden", säger Forsman. "Våra kunders utmaningar blir alltmer komplexa. Vi måste använda vår expertis för att arbeta hand i hand med våra partners och kunder och fortsätta att uppfinna nya sätt att möta dessa utmaningar."
One of the Sandvik engineers testing the strength of the guitar on various items of old furniture and equipment.
Live, i konsert
När gitarren var färdig gav Sandvik den till Malmsteen för att spela på. På en klubb i Florida spelade Malmsteen flera låtar och började sedan svinga gitarren mot förstärkare, scenkonstruktioner och golvet, och gjorde sitt bästa för att krossa den.
"Den här gitarren är en best!" sa Malmsteen efter att ha gett upp försöken att förstöra den. "Sandvik är uppenbarligen på toppen av sin förmåga. De lägger ner arbete, de gör sina timmar. Jag kan relatera till det. Resultatet är fantastiskt. Jag gav allt jag hade, men det var omöjligt att krossa den."
Titta på filmen "The Smash-Proof Guitar, testad av Yngwie Malmsteen":
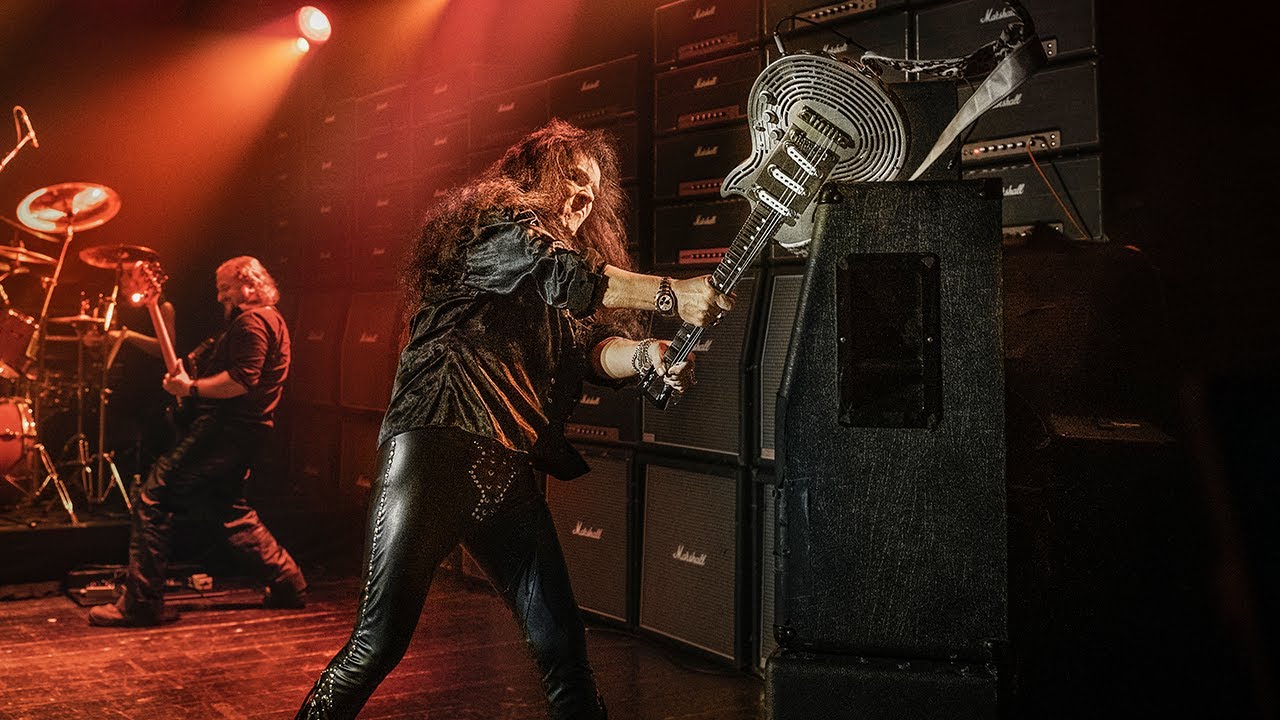
Nyfiken på att ta reda på mer?
Du hittar mer information om de olika tekniker som används när du bygger gitarren på nedanstående Sandvik-webbplatser:
Skärande bearbetning av metall: sandvik.coromant.com
Additiv tillverkning: additive.sandvik
Rostfria stål: material.sandvik