3D printing and other Sandvik breakthroughs with Johan Wallin
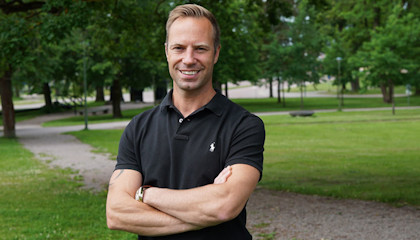
Johan Wallin tells the story on how Sandvik became the first company to 3D-print super-duplex stainless steel at an industrial scale and how that can affect different industries. “Since the biggest cost in the offshore industry is a standstill, they need to have huge stocks of spare parts. If you can produce the spare parts by additive manufacturing when you need them, you will reduce stock, reduce the networking capital and save a lot of energy,” he says.
Johan Wallin is product manager at Sandvik division Additive Manufacturing. In this episode he explains why super-duplex stainless steel is a super material, why it is so difficult to 3D print and how Sandvik succeeded.
“You can also switch from less noble materials in your components and use super-duplex materials that will last for 30 years instead of ten years. Then you don’t have to change and scrap the spare parts as often and when this spare part is due after 30 years, you can recycle it, make it into powder and 3D print a new one,” Johan Wallin says.
He also talks about the great sustainability gains with additive manufacturing and opportunities for the future.
Meet Sandvik Podcast
In each episode of the podcast Meet Sandvik you will meet different persons that give their perspective on Sandvik. Sometimes it´s an employee telling his or her story. Sometimes you will meet experts discussing how a hot topic can affect Sandvik.