Winners of the Sandvik Sustainability Award 2021
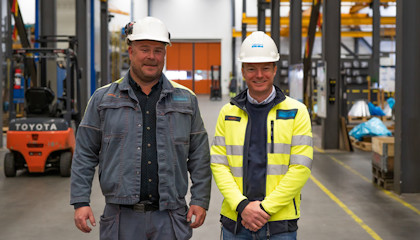
The main benefit for both us and our customers is that we can use worn-out parts to produce new and hence, reduce the need for virgin material, says Anders Åkesson. Jörgen Petersson adds, This, in combination with fine-tuning our recipes for the furnace and by implementing a new way of working, we have now reached more than 90 percent circularity in our production.
In this episode, Anders Åkesson and Jörgen Petersson tell the fascinating story of how a savings program resulted in the world’s most sustainable manganese foundry. And how the teamwork at the Svedala site has been key in closing the loops of the entire value chain, from raw material to production, to the customer and back again.
“We help our customers become more sustainable and that is a business advantage for both the customer and for Sandvik", Åkesson says.
Anders Åkesson and Jörgen Petersson also walks through the process of how every piece of metal scrap at the site, from large pieces of wear parts to small metal chips rendered from the machining are analyzed and re-used and how the Svedala site can now leverage the different alloys in all types of manganese steel. A fascinating journey that is inspirational to both industrial companies and others.
Meet Sandvik Podcast
In each episode of the podcast Meet Sandvik you will meet different persons that give their perspective on Sandvik. Sometimes it´s an employee telling his or her story. Sometimes you will meet experts discussing how a hot topic can affect Sandvik.