Startups rewarded
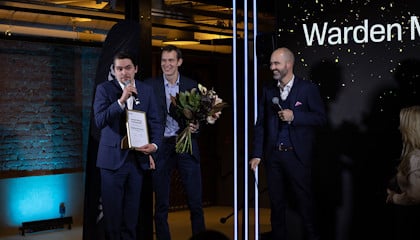
Talented digital innovators from around the world took up the challenge to develop concepts that make mining and manufacturing safer, smarter and more sustainable.
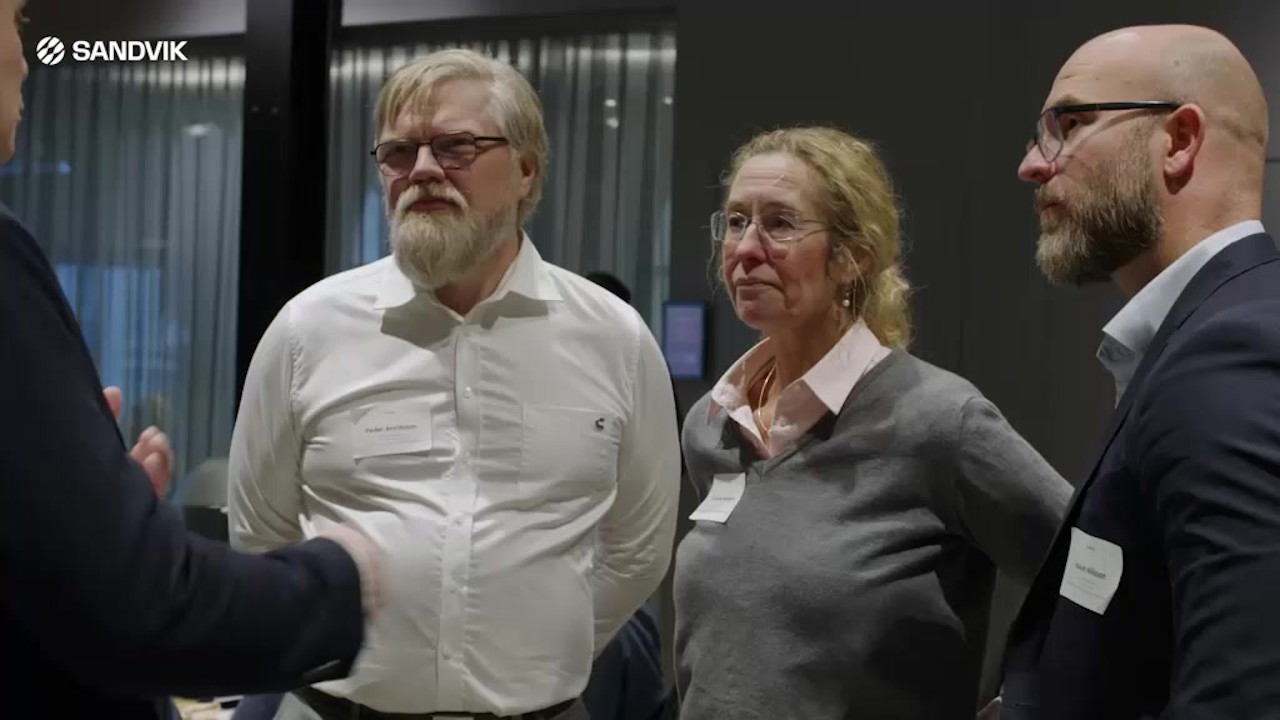
The Startup Challenge is a worldwide call for innovative startups to interact and collaborate with Sandvik experts. The challenge is run by Sandvik together with its partners SynerLeap and Microsoft. The nine finalists in this year’s Challenge took to the stage in Stockholm on November 9 to present their solutions, after which the jury convened to pick the winning teams.
Pasi Kangas, Head of Technology at Sandvik Additive Manufacturing and Jury Chairman explains the reason behind it: “The ongoing digitalization of mining and manufacturing requires advanced, connected systems. We are looking for the brightest minds and best ideas for software and equipment that let Sandvik and its customers work faster, more sustainably and more efficiently,” he said. “I am very happy about the great response and quality of the applications, and the enthusiasm and energy surrounding this call, both from the Sandvik teams and all startups that we have collaborated with.”
Each of the three Sandvik business areas offered a unique challenge. The winning startups, from Finland, Luxemburg and the US, received Swedish crystal artwork and funding up to USD 30,000 to collaborate with Sandvik on the development of a Minimum Viable Product (MVP) that can be productized and offered to Sandvik customers.
Dynamic cutting recommendations
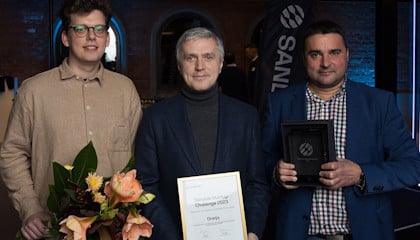
The challenge offered by Sandvik Coromant was to develop software thatenables dynamic recommendations within industrial metal-cutting applications. Finland-based startup Dreija, with Oleg Shadrunov, Ilmari Junttila and Dmitrii Shustrov, won the challenge.
The team from Dreija had developed an app using dynamic cutting data and machine learning that recommends machine settings that fit the specific task and component to be manufactured. “Thanks to AI, our software learns faster than a person and is able to analyze dependencies between thousands of different parameters, from speed and temperature to raw material characteristics, to arrive at an optimized setting for indexable tools,” explained Shadrunov. “This results in increased sustainability from less waste and lower energy consumption, less machine wear and faster setup times.”
Our software can compensate for years of hands-on learning.
Shustrov pointed out that the solution is particularly useful for new employees who lack experience from the machining sector. “Our software can compensate for years of hands-on learning.”
The next six months will be spent developing a prototype with Sandvik and testing it with select customers.
Enhanced industrial process insights
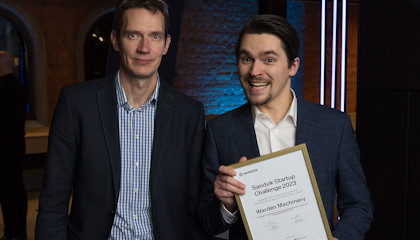
Sandvik Rock Processing Solutions invited solutions to evolve individual equipment insights to drive plant efficiency and sustainability improvements. Inspection of the crushing and screening of excavated rock along conveyor belts is crucial to the stability of operations and quality of final output.
Luxemburg-based startup Warden Machinery, with Mikhail Kiriukhin and Vladimir Bashkov, won the challenge with a solution based on cameras, sensors and AI-enabled software for continuous inspection of crushed rock material. “It gives insights that allow users to optimize the efficiency of rock processing,” says Kiriukhin. “Manual inspection of crushed material, particularly in remote locations, is a tedious task and it's easy to lose focus. Our solution enables a stabilized feed of rock that reduces the downtime of rock processing operations.”
It gives insights that allow users to optimize the efficiency of rock processing.
To put it simply, the software may be compared to facial recognition software, applied to crushed rock instead of human faces. Following a joint development of an MVP with Sandvik, the solution promises to significantly reduce the sustainability footprint of operators and improve the guidance provided to them. As Kirukhin puts it: “It’s time to rock!”
Safety first with automated anomaly detection
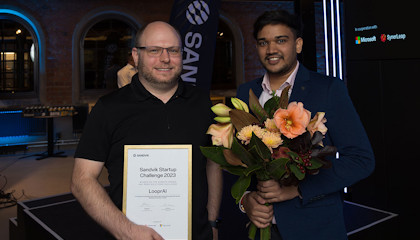
The drill and blast method is commonly used in underground mines. Due to the dangerous nature of blasting, it is forbidden for people to re-enter the tunnels right after the blast because of fumes, dust, the risk of misfire and the possibility of changes to the ground conditions that could make the area unstable. Sandvik Mining and Rock Solutions was looking to develop an automated solution for detecting possible anomalies after blasting in a tunnel.
The winning startup, Loopr AI from Seattle, US, had developed a solution for real-time detection of anomalies in the mine, based on cameras and sensors plus AI-enhanced software that is better equipped to analyze signs of anomalies than even the trained eye of a pro. Since digital equipment doesn’t mind hazardous conditions such as fumes, there is less downtime following each blast.
The safety aspect is the unique selling point of our solution, but it also reduces the downtime required after a blast.
“AI can aid humans by analyzing multiple video streams in real time and it never gets tired, whereas a person may find it hard to spend an entire shift staring at a video and reading sensor data without losing attention,” explained Loopr AI’s Eric Johnston. “The safety aspect is the unique selling point of our solution, but it also reduces the downtime required after a blast by enabling a quicker all-is-clear signal.”
During the jury meeting, it became clear that the Sandvik team in charge of the mining challenge was interested in engaging with yet another solution as well. Kangas explains why. “The company Sensorise was selected for further collaboration with Sandvik on their solution, which includes intelligent anchors continuously monitoring rock face and bolted equipment combined with a system that stores, displays, analyzes and distributes information from the intelligent anchors”.