How AI is transforming factories
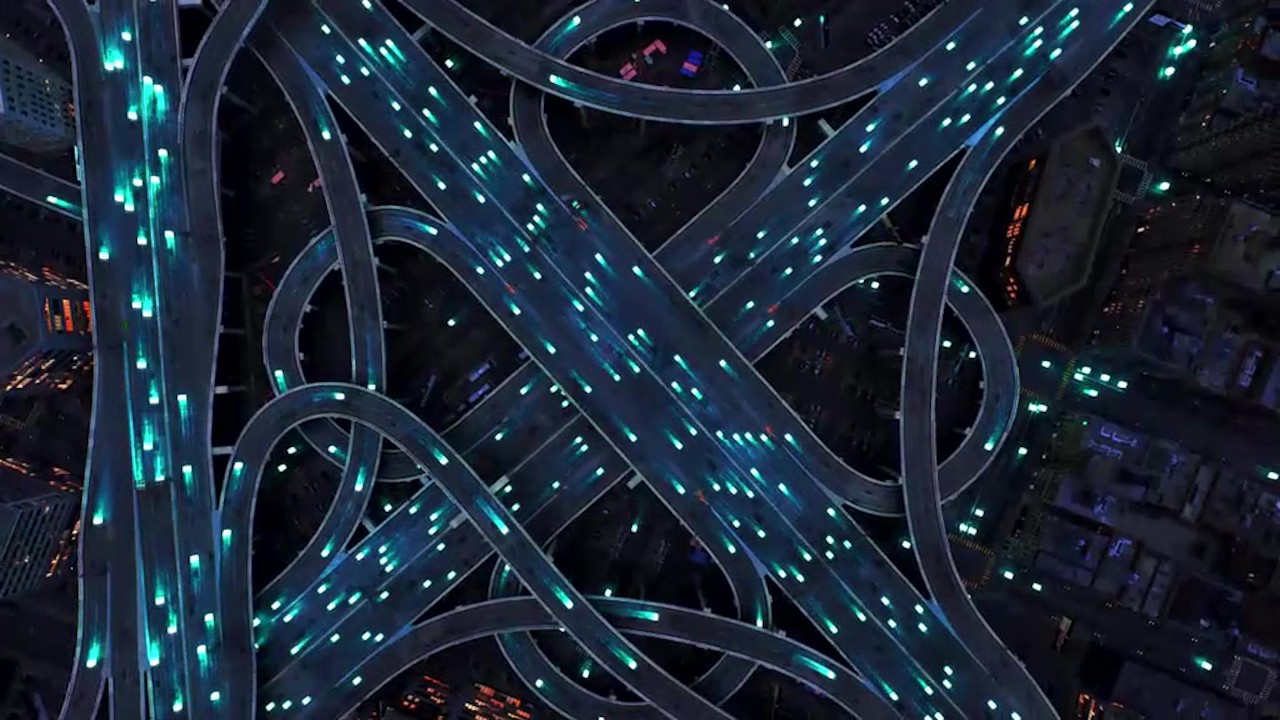
Artificial intelligence is already having a major impact on manufacturing operations around the world. From quality control to forecasting and product design, manufacturers are using AI systems to change the way their factories work.
These days, when a new vehicle rolls off the line at any major European car manufacturer, chances are that an AI system was involved in the production process.
Machine learning is quickly revolutionizing the way products are made across industries as manufacturers utilize the benefits of artificial intelligence to perform tasks faster and more accurately than any human could.
The difference with AI is the scale of automatization that you can achieve, which leads to increased efficiency for the entire factory.
According to a study by Capgemini, more than 50 percent of top European manufacturers are currently implementing AI in some way. Germany leads, with 69 percent of manufacturers using it. In Japan that figure is 30 percent and in the United States it’s 28 percent. China brings up the rear with 11 percent.
This is only the beginning, however. Most experts are already talking about Industry 4.0, considered a fourth industrial revolution in which machine learning algorithms create autonomous systems that make the smart factory a reality.
“AI will doubtlessly speed up the automatization process in manufacturing,” says Robert Luciani, Executive Advisor at the AI Framework in Stockholm. The difference with AI is the scale of automatization that you can achieve, which leads to increased efficiency for the entire factory.”
How does AI work?
A standard computer algorithm contains a specific set of programming instructions that tells the system exactly what to do, and in what order. An AI algorithm, however, is designed to learn the best way to perform a task without using specific instructions. Instead, it uses input data and feedback to develop a model, often through millions of repetitions of trial and error.
AI can study values from dozens of components and see well ahead of time if there’s a problem brewing.
The chess program Alpha Zero is one example of how AI can quickly outperform humans and traditional computer programs. The developers at DeepMind trained Alpha Zero by simply teaching it the rules of chess, without giving it any strategic advice. The program then played millions of games against itself, improving its understanding each time. Within hours, it was able to beat the strongest traditional chess programs — and humans — with a style of play that took top grandmasters by surprise.
AI systems for manufacturing can use self-learning in a similar way. Mitsubishi, for instance, has developed an AI system that teaches robots new tasks by letting the machines develop optimal actions through trial and error.
Improving quality control
Today the most common applications of AI in manufacturing are for quality control and predictive maintenance; many companies also use it in production, product development and supply chain management.
In predictive maintenance, AI systems can monitor input from a multitude of machines and systems for early signals that something may be about to break down. They can then take action, preventing factory shutdowns.
“AI can study values from dozens of components and see well ahead of time if there’s a problem brewing and whether preventive measures are needed,” says Luciani. AI is especially good at quality control as it can use automated visual inspections to detect minute flaws that the human eye may not spot.
Japanese tire manufacturer Bridgeston uses an AI tool with sensors that inspects 480 different physical items to ensure that all tires are assembled in optimal condition.
BMW uses automated image recognition in which the AI application compares an ongoing production sequence with hundreds of other images of the same sequence to make sure that all parts are being mounted correctly. Volvo deploys camera-based AI tools that inspect the finished vehicles, including the undercarriage and tires. These tools can also be used by car repair shops to find issues.
Finding better design solutions
AI is also increasingly being used in the design process, especially when it comes to additive manufacturing (3D printing). In what is called “generative” design, the AI algorithm is told the design goals and parameters to follow, such as materials and cost constraints, and the algorithm then tries out thousands of different design options to find the best one.
General Motors used such an AI tool to design a 3D-printed seat bracket that consolidated eight different parts into one part that was 40 percent lighter and 20 percent stronger than the previous one.. Other popular uses of AI include forecasting demand for certain products, which can help optimize production schedules, inventories and raw material procurement. But hurdles remain when it comes to spreading the use of AI.
One area where I think AI will be used is in made-to-order products.
There is still a level of skepticism surrounding “intelligent” machines, which means that any mistake made by an AI system is often seen as more serious than mistakes made by humans — even if they occur much less frequently.
AI systems can also be very expensive to develop and are only as good as the data that is fed into the algorithm. Many companies still don’t have the level of expertise needed to scale AI solutions across their manufacturing network.
So far, most uses of AI in manufacturing are taking place “under the hood” in a way that consumers don’t see or experience. But Luciani thinks that may change in the future.
“One area where I think AI will be used is in made-to-order products such as tailor-made clothes, where AI can help measure the right fit for suits and shoes,” says Luciani. “It can really be used for anything.”