Digital transformation of the manufacturing industry
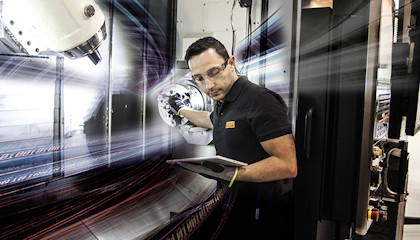
To be in the forefront of the manufacturing industry, corporations need to adapt to the ongoing digital transformation. For Sandvik, it is a means to keep delivering productivity for its customers.
Digital manufacturing offers huge potential – to improve productivity, reduce lead times, reduce working capital and improve cash flow. But how will the smart manufacturing of the future work?
In the future all machines, from milling machines to welding robots, will be networked with one another, according to German research organization Fraunhofer. Every workpiece will have its own embedded system, storing various pieces of information on, for example, the customer, the workpiece’s desired configuration and its destination. It will be possible to uniquely identify and localize raw parts.
Workpieces will communicate.
Not only will they know the processing steps necessary, these parts will also be networked with the production machines and will be able to communicate with one another to decide exactly when they are to undergo which production step.
A self-organizing process
In the future, the entire line will no longer stop when a given station fails. Instead, workpieces and machines will work together to replan the processing sequence. The result is a “self-organizing” adaptive manufacturing process that no longer requires constant human intervention, while remaining under human control.
The result of the digital transformation is a process that no longer requires human intervention.
In order for smart production to run smoothly, the humans and robots involved have to continuously report exactly what they are doing and, for example, how long parts subject to wear have until they fail. Everything taking place in the real factory will be represented in parallel in the virtual factory. Experts refer to this connection between the real and virtual worlds as a cyber-physical system, or CPS.
The economy is hoping for several advantages from the digital transformation of industry, not least that the flexible factory of the future will make it possible to manufacture according to customer preferences and make production changes ranging up to the integration of new machines at any time without substantial effort. Machine utilization levels will be higher, the consumption of resources will drop, and there will be fewer rejects.
There is good news for the smaller enterprises: advances in the past decade have made factory optimization better, easier and more cost-effective.
So far, larger manufacturing enterprises have been the main beneficiaries of smart-manufacturing innovations, while smaller manufacturers have lagged behind.
“The challenge is helping smaller manufacturers obtain tools that are neither too expensive nor too complex to collect the necessary data themselves,” says Stephan Biller, CEO of Advanced Manufacturing International Inc. in the February 2022 edition of Smart Manufacturing magazine. “But there is good news for the smaller enterprises: advances in the past decade have made factory optimization better, easier and more cost-effective.”
Digital transformation requirements
The digital transformation will require new skills and competences from the workforce, an issue addressed by the World Economic Forum (WEF) in a recent report.
“The new world of work in the fourth industrial revolution is rapidly becoming a lived reality for millions of global workers and companies,” says Saadia Zahidi, a member of the WEF’s managing board and head of its Center for the New Economy and Society. “The inherent opportunities for positive outcomes for workers, the economy and society are enormous, yet crucially depend on bold action from all concerned stakeholders to instigate reform in education and training systems to prepare workforces for the skills of the future.”
Upskilling and reskilling
Businesses around the world are increasingly taking the lead in upskilling and reskilling their own workforces as well as their surrounding communities, equipping what they hope will be the next generation of their workforce with skills for the future.
Closing the skills gap in Pune, India.
One example is Sandvik India, which is providing young people with a springboard for a career in manufacturing and access to some of the industry’s most cutting-edge technologies. “The younger generation of India holds significant potential to close the skills gap, once they are trained with the technical knowledge needed for modern jobs,” says Kiran Acharya, managing director of Sandvik Asia. “India has entered a golden period that’s set to last until 2040, due to a shift in the population’s age structure.”
Sandvik Coromant has partnered with the Indian government to establish the Sandvik Coromant School of Manufacturing Excellence to train Indian youth from underprivileged and marginalized backgrounds. Based at the Industrial Training Institute in Pune, the school educates students on advanced metal-cutting techniques.