Recycled materials turn wine to roads
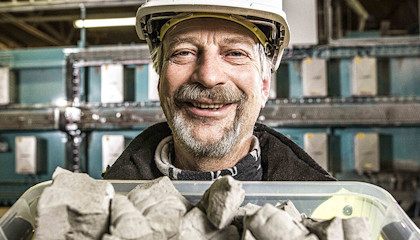
Norwegian company Glasopor is one of few manufacturers in the world that produce foam materials from recycled glass. The company has boosted its profitability and eliminated its carbon footprint by switching from gas to electricity based on a Kanthal® electric heating system.
Nestled in the rolling hills of the Skjåk countryside just west of Oslo is the Glassit factory, one of Europe’s most innovative glass recycling works. This plant, owned by Glasopor, recycles some 18 million wine bottles and other glass products per year and turns the waste into a granulated high-tech foam material.
We have reduced our CO2 emissions to zero.
This lightweight foam glass is used mainly as filler in the construction of roads and railways, where it is especially effective in poor ground. It is also widely used as an insulation material in buildings. Glasopor’s premium foam glass is 100 percent recyclable and consists of 80 percent air, which results in a bulk weight of 180 kg/m3.
With recycled materials at the heart of production, Glasopor chose Kanthal to help improve its footprint further and convert from gas to electric operations.
Profiting from recycled materials
To improve its environmental performance and reduce costs, the company engaged Kanthal, a Sandvik division, for a complete process conversion from gas to electric heating.
Since the company was founded in 2002, Glasopor’s sales have gone from strength to strength, but as a modern recycler it was not entirely at ease with its own internal performance. Its gas consumption, and therefore its energy cost, was high and so too were its CO2 emissions – around 4,000 metric tons per year.
Our aim was to reduce our energy consumption by 28 percent.
After a thorough review of its operations, the company decided to take the radical step of switching its energy source from gas to electricity, based on Kanthal® electric heating technology, and it has never looked back.
Although the switch itself from gas to electricity entailed a substantial cost saving, Glassit wanted a powerful heating system that it could rely on for its glass foaming process. In addition, the plan called for the upgrade of furnace zones as well as service and maintenance to keep the system working effectively and efficiently far into the future. The choice was Tubothal® heating elements from Kanthal, recognized worldwide for its superior efficiency.
More succesful than imagined
The complete conversion from gas to electric was managed on-site in Norway. The team designed and simulated the conversion, calculating the required power and element temperatures. In the planning process, technicians from Kanthal also provided a payback calculation to facilitate the upgrade of three zones in the furnace.
The decision to switch from gas to electric turned out to be more successful than anyone had imagined. Glasopor Development Manager Svein G Lund explains: “In calculating this conversion we saw it as something of a high-risk project for us,” he said. “Naturally we wanted to improve the environmental side – because of course that’s very important for us – but we also wanted it to be beneficial in terms of our future earnings.
We think this project will help us to maintain our position as the leading manufacturer of glass foam products.
“Our aim was to reduce our energy consumption by 28 percent. Today our research shows that the real reduction in energy is more like 37 percent – even higher than we expected, which is fantastic! And on top of that, we have reduced our CO2 emissions to zero.”
Lund adds that the new system is in the spirit of innovation that has permeated the company’s development since its inception. It also fits in with Glasopor’s policy to use local water power resources rather than pump gas from the North Sea.
“Innovation is the driving force in this company and the key to our success,” he says. “We think this project and the Kanthal system will help us to maintain our position as the leading manufacturer of glass foam products, and that’s something we are looking forward to telling the market about.”