A win-win race
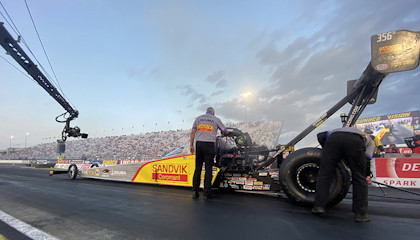
The carmaker Henry Ford once said that, “Auto racing began five minutes after the second car was built.” Adaptability and automobiles go hand-in-hand, and precision parts manufacturer Don Schumacher Motorsports (DSM) collaborates with Sandvik to keep winning on the racetrack and expand into industries as diverse as aerospace and defense.
In September 2020, Matt Hagan gave Don Schumacher Racing (DSR) its 350th victory in the final round of the Lucas Oil National Hot Rod Association (NHRA) Summernationals at the Lucas Oil Raceway in Brownsburg, Indiana, US. Hagan raced to victory in his drag racer, or Funny Car, which can race from zero to 330 miles per hour in less than 3.7 seconds.
When relying on an outside partner for anything, there is a question of trust.
DSR has scored victories behind the scenes too. In 2018, the company acquired the ISO 9001:2015 certification in recognition of its quality management and sustainability initiatives, demonstrating that the company’s operations fit-in with United Nations (UN) sustainability goals.
The shop’s other win has been a victory against the business challenges of COVID-19. In just two years, the machine shop — founded to support the company’s drag race program — has successfully diversified into a range of sectors, from defense and aerospace to commercial applications.
Scalable solutions
Now, says Chad Osier, Vice President at DSM, the Brownsburg machine shop is the only of its kind in the Midwest that offers such a high degree of precision engineering, for such a wide range of sectors. “Racers are engineers, and precision engineering extends to everything we do. This expertise and the right tools allow us to hit the required levels of precision and quality when building nitro blocks for drag racing that produce 11,000 horsepower.
“Now we can bring that same precision to bear on competitive quality and scalable solutions for the defence, aerospace, commercial, motorsports and automotive industries.”
Minimizing scrap
How has DSM achieved all of this in such a short time? The answer lies in DSM’s choice of tooling partner, the Sandvik division Sandvik Coromant. “We're obviously in the business of racing,” says Osier, “but we are also in the business of making profit. Tool wear is a big part of that. We want to make sure we’re minimizing as much waste and scrap as possible. The tooling and equipment we use from Sandvik goes hand-in-hand with how we operate.”
DSM also sought help from Sandvik to become, what Osier describes as, a “full-on kind of general engineering machine shop.” That is, one that can build project products ranging from small specialty fasteners and the right-mass nitro engine blocks, to bespoke aluminum parts for defense and aerospace. From rapid prototyping all the way to mass production.
“When relying on an outside partner for anything, there is a question of trust,” says Osier.
Brian Flores, Channel Manager for the Eastern United States at Sandvik Coromant, agrees: “We help DSM in several ways, from supporting the local sales engineers to helping DSM’s automotive specialists and process improvement experts. That includes working closely with its team of specialist programmers to develop precision parts like piston heads or engine blocks out of tough-to-machine solid aluminum billets.”
Very complex processes
“These machining processes are very complex,” explains Flores. “The tooling from Sandvik is used in the lathes and mills we use, made by Okuma America, which allow us to get the machined parts up to the necessary quality standards. This is where harder-wearing tools prove critical.”
Sandvik offers the engineering support to allow us to tackle any project.
For these applications, DSM relies on Sandvik Coromant tools like CoroMill® 390 shoulder milling cutters designed for versatility, with ramping capability for mixed production. “We look for tools that will produce consistent and repeatable parts, and minimize our scrap and our cycle time,” explains Osier. “So, the biggest thing I get on sustainability is how we're able to maximize our output and reduce our material scrap in automated processes.”
Osier estimates that DSM’s production is now divided roughly 50-50 between its racing obligations and its general precision engineering contracts. The manufacturer will continue to build on this going forward, including investing in 3D metal printers.
“Sandvik has consistent products that are at the top of the market and it offers the engineering support to allow us to tackle any project,” says Osier.
It looks as if DSM will continue leading the race in a range of industries for many years to come.
Want to know more?
We make the shift – advancing the world through engineering
Through our diverse teams, strong culture and leading-edge skills we enhance productivity, efficiency and sustainability in a world that needs to evolve. Our role is clear – through every action, every day, we make the shift and advance the world through engineering.