Titanium powder for sustainable manufacturing
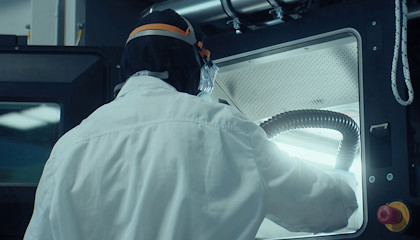
Powder metallurgy is since many years labeled as a ‘recognized green technology’. Titanium powder, with its unique material properties, makes it even more sustainable when used in game-changing technologies like additive manufacturing (3D-printing).
In the “Powder Metallurgy – Intrinsically Sustainable” report, the Metal Powder Industries Federation compares the 17 manufacturing steps that are required to produce a truck gear using subtractive machining with the mere six that are required using a powder metal-based process – with each less step bringing a saving in energy consumption.
Powder-based net-shape technologies like additive manufacturing also make it possible to merge several components into one – reducing assembly steps and thereby energy consumption. In addition, it often minimizes the use of cutting lubricants and cleaning fluids, although one of the strongest sustainability arguments for additive manufacturing is reducing material waste.
“When printing a component, approximately 95 percent of the powder you put into the process is used, the rest we can recycle in a new melt. Compare that to traditional manufacturing where you start off with a chunk of material and reduce large amounts of chips,” says Mikael Schuisky, Head of Business Unit Additive Manufacturing within Sandvik.
Combining additive manufacturing with titanium can create enormous sustainability advantages.
Another environmental advantage is that the production can be undertaken locally, which removes further steps in the supply chain – and reduces transportation.
“You go directly from a digital design to a three-dimensional product. And, if you locate production close to where it’s needed, you can cut down on storage, packaging and transportation of parts,” Mikael Schuisky says.
A shift towards lighter components
Sandvik’s recently launched Osprey® titanium powders are supporting the growing trend of 3D-printing of titanium parts – and the shift towards sustainable manufacturing and lighter components. Apart from reducing material waste, additive manufacturing also enables new design freedom. It opens up for titanium usage in other industries beside aerospace and medical – such as automotive and tooling. For example, CoroMill® 390, a light-weight milling cutter produced by additive manufacturing, is more than 80 percent lighter and up to 200 percent more productive than a subtractive version of the tool.
“Combining additive manufacturing with the opportunities that comes with a light and strong material like titanium can create enormous sustainability advantages. Weight reduction, for example, is an everlasting issue for the aerospace industry, driven both by fuel cost and carbon footprint. Each kilogram of weight loss on an airplane saves 3,000 US dollars per year in fuel – and can make a great difference for the planet,” says Keith Murray, VP Global Sales, Sandvik Additive Manufacturing.
Read more about titanium powder on our website metalpowder.sandvik
A recognized green technology
- Powder metallurgy is a “recognized green technology”.
- Almost no waste in shaping of parts – and the surplus powder can be reused.
- The net-shape capability of powder metallurgy (in applications like Additive Manufacturing or Metal Injection Molding) means that great energy efficiency can be achieved, by eliminating manufacturing steps.
- Osprey® metal powders contribute in making our customers’ processes and end-products more sustainable.
- Eliminating waste (e.g. when printing a component, about 95% of the powder is used; the rest can be recycled in a new melt).
- Possibility to produce lighter components – reducing fuel consumption and
CO2-emissions in e.g. aerospace or automotive. - Possibility to merge several components into one – reducing assembly steps and
thereby energy consumption. - Minimizes use of cutting lubricants and cleaning fluids.
- If you locate production close to where it’s needed, you can cut down on storage, packaging and transportation.
- Part of the raw material for Osprey® metal powders consist of recycled scrap metal – and the manufacturing is based on 100% renewable energy.