Designing materials at atomic level
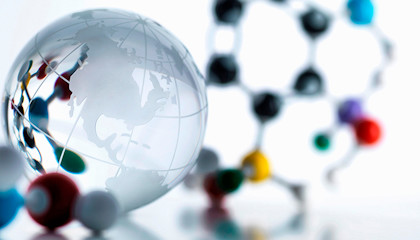
To develop the materials that society will demand tomorrow, we need to think radically and collaboratively. With its world leading materials expertise, Sandvik is well positioned to help create tomorrow’s world.
Sandvik has been developing new materials for more than 150 years. Today it is one of the world’s leading developers of new materials. The company knows that staying ahead of current trends is essential to meeting customer as well as societal demands.
Marco Zwinkels, Director R&D Technology Platforms at Sandvik Coromant, says industry demand for new materials is driven primarily by the aerospace and automotive sectors and the push for more sustainability across manufacturing.
From the opportunity side we drive long-term research in-house, often in cooperation with institutional and academic partners.
This demand, Zwinkels says, presents similar challenges for the development of new materials by Sandvik to be used in products across industry and manufacturing as it does for the development of Sandvik’s cutting tools.
“The trend for weight reduction in all forms of transportation is resulting in an ever-increasing use of fiber composite materials and lightweight materials such as titanium,” he says. “We are seeing an increase in aluminium components, driven by the development of electrified vehicles. At the same time, more advanced heat-resistant superalloys are now being used for turbines in the aerospace industry. These are often very tricky to machine, which puts higher demands on our tools.”
Another driver for the development of new materials in the machining solutions area comes from several issues associated with cobalt, one of the key constituents of cemented carbide, the main material used in metal and rock cutting tools.
Cobalt is becoming more problematic, Zwinkels says. “Cobalt has been reclassified as more hazardous than before, and occupational exposure limits have been lowered,” he explains. “In addition, it is mined at or close to conflict areas. Furthermore, it is used in car batteries, so with the electrification of cars there is a risk it will become scarce.”
Trying to understand future needs
Zwinkels says that Sandvik has both a challenge-driven and an opportunity-driven perspective when it comes to developing new materials.
“From the opportunity side we drive long-term research in-house, often in cooperation with institutional and academic partners,” he says. “We probe and track the development of new materials in academia. The need side comes from customer requests, market trends and industry developments. The essential input comes from our global sales, engineering and specialist network as well as from the business intelligence function. We try to understand from this what kind of material development will be necessary for the future.”
We are now at atomic levels in designing our materials, allowing us to create new compositions of existing materials.
Susanne Norgren, Group Expert Materials Design at Sandvik, is also an associate professor in Applied Materials Science at Uppsala University. For her, the most exciting development in materials science comes from revolutionary new processes.
“Additive manufacturing and the further development of integrated computational materials engineering are methods where materials are digitally optimized in order to achieve certain desired properties. We can also develop and design materials and components in new and faster ways,” she says. “The 3D-printed spacecraft landing gear for SpaceX is an example where this method is used in proceeding from atomic level to finished product.”
Moving atoms about
Zwinkels agrees. “Materials science has become very mature,” he says. “We are now at atomic levels in designing our materials, allowing us to move atoms about to create new compositions of existing materials. Computational modeling allows us to see what kind of new compositions could be possible and what would be needed to realize those.”
Another key advantage of additive manufacturing, Norgren points out, is that it allows engineers to remove waste materials from the process, making materials lighter and therefore more sustainable. “I think all of Sandvik’s customers will benefit from this,” she says. “And Sandvik will benefit internally too in terms of efficiency. Sandvik is very well equipped when it comes to 3D printing machines and know-how.”
Sandvik is the leading global player when it comes to recycling cemented carbide.
Perhaps the only way that a sustainable world can really be achieved, though, is through recycling. And this is also something that material scientists are increasingly exploring more, helped by the new computational processes.
“Driven by the increasing scarcity of cobalt and many other materials, as well as the need to reduce our carbon footprint, we must move toward 100 percent usage of recycled raw materials in our products,” Zwinkels says.
“Sandvik is the leading global player when it comes to recycling cemented carbide. A significant amount of the materials that we sell comes from recycled tools, which we buy back and convert into new material. We have done that successfully for many years, and this will become increasingly important.”