Powder metallurgy makes furnaces eco-friendly
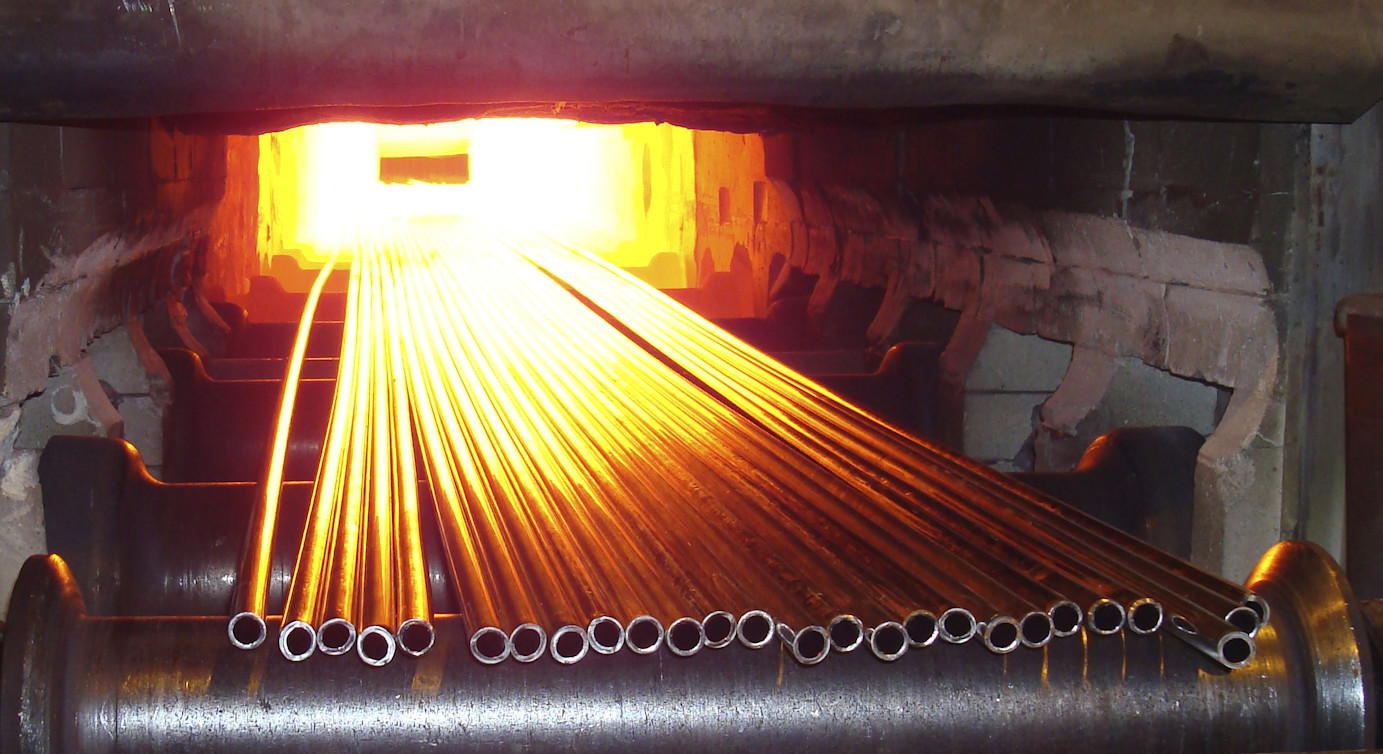
Sandvik’s powder metallurgical materials, with their unique combination of high oxidation resistance and form stability, boost both productivity and energy savings. They also reduce maintenance needs for those customers with demanding high-temperature manufacturing processes.
Efficient heat treatment is vital in the production of everything from integrated circuits for smartphones to solar cells and steel- and aluminum-based products. One challenge that manufacturers are constantly grappling with is that industrial ovens have to cope with the extreme heat required for these processes, often up to 1,250 degrees Celsius.
“A common problem is that the construction components within heating systems deform over the course of time,” says Bo Jönsson, technical specialist at Kanthal, the part of Sandvik Group that develops products and systems for industrial heating. “For a material to function properly at high temperatures, two essential properties are required: good form stability and oxidation resistance.”
Boosts energy savings
Materials that are traditionally used in these types of furnace applications are often nickel-based, which provide good form stability but limited oxidation-resistance, ”he explains. However, conventionally produced materials – based on iron, chromium and aluminium – have excellent oxidation properties but relatively low form stability.
For a material to function properly at high temperatures, two essential properties are required: good form stability and oxidation resistance
“We’ve put a lot of work into finding solutions that help customers with this dilemma,” Jönsson says. “The Kanthal APM™ and Kanthal APMT™ materials combine uniquely high oxidation resistance and form stability. The key to successfully developing these properties was the use of powder metallurgy to obtain an optimum microstructure in the materials.”
Jönsson explains that the powder metallurgy technique has made it possible to structure the metal with billions of small particles, substantially boosting its strength at high temperatures. The materials are now used in applications such as heating systems for industrial furnaces and other demanding uses.
“One example is furnace rollers for continuous annealing lines made from Kanthal APMT™, that eliminates the need for water cooling,” Jönsson says. “This provides significant energy savings and environmental benefits. In many cases it has also been possible to reduce maintenance needs and boost productivity as a result of increased process temperatures and fewer shutdowns.”
We’ve put a lot of work into finding solutions that help customers with this dilemma
Jönsson sees significant opportunities for expanding the use of powder metallurgy materials. For example, Kanthal APMT™ has contributed to Sandvik now being involved in a number of projects relating to a future fossil-free energy supply.
“The combustion of bio-based fuels generates corrosive environments that our materials have demonstrated good abilities to resist,” Jönsson says. “They could even be of use in the next generation of nuclear power plants. And for large-scale concentrated solar power to be cost-effective, new materials are needed that can handle and store solar energy at higher temperatures.”
Read more about Kanthal APM™ and Kanthal APMT™ materials on the Kanthal website