Smarter solutions through digitalization
Digital developments are creating a host of new opportunities in industrial applications and processes. For Sandvik, this means an accelerated pace of launching new digital solutions that contribute to increase safety, reduce environmental impact and optimize efficiency.
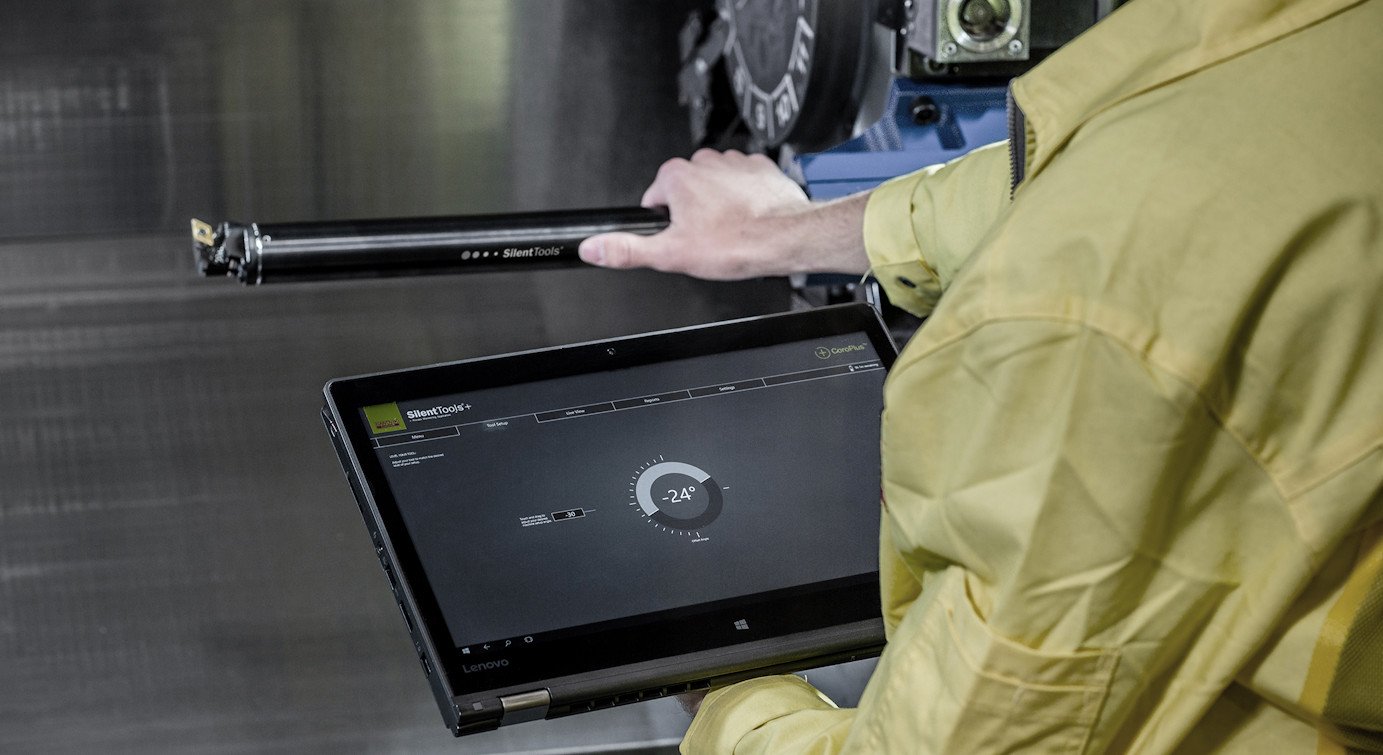
Developments are progressing rapidly, and what many are calling the fourth industrial revolution is starting to take shape, with interconnected machines communicating and able to take decisions and integrate with their environment.
Five areas or trends where these opportunities are particularly evident are:
- Big data analytics
- Cloud services and increased mobility
- The internet of things and connectivity
- Artificial intelligence and augmented reality
- Automation and robotics
Digitalization is making it possible to identify smarter and better products and solutions, to optimize the way in which companies take their products to market and offer services. And of course digitalization also enables companies to become more efficient and profitable.
Software gaining ground
In the metalworking sector, for instance, it is estimated that software services will quadruple between 2015 and 2025. Sandvik is therefore focusing on developing and expanding its digital machining offering to the metalworking industry.
In 2016, Sandvik launched CoroPlus®, a range of services, software and sensor-based tools that for example can monitor the various stages of a machining process and help boost productivity. A combination of software, connected tools and data analysis of machining performance, enables process optimization.
CoroPlus® also comprises another strategic area – computer-aided manufacturing (CAM). CAM software analyses a CAD model and establishes a process for manufacturing components. CoroPlus® ToolLibrary and CoroPlus® ToolGuide give manufacturers access to a digital tool library and cutting data, allowing cutting data recommendations to be integrated directly in the CAD/CAM environment.
Additive manufacturing is growing
An additional strategic growth area is additive manufacturing, also known as 3D printing. Metal additive manufacturing is becoming more widely used and is starting to be established as a production method. For instance, a new model of Airbus plane has up to 1,000 parts created through additive manufacturing.
This new method is in response to demands for lower costs, shorter lead times and greater efficiency, and in particular for lighter, stronger, higher-performance products.
Digital mining solutions
The mining industry can also benefit from digital solutions. Key drivers in this area include improved safety and the need for greater productivity and efficiency.
AutoMine™ equipment automation solution offers connected, automated and autonomous equipment, providing mines around the clock with data on the condition and performance of equipment via the My Fleet web portal. The portal also provides data analysis and information on maintenance schedules, and can be used to order parts and service kits.
There are currently over 25 installations with more than 150 automated items of equipment in operation and there are numerous examples of how this has increased production, cut operating costs, reduced maintenance costs and extended the life of equipment.
Sandvik also offers data-based productivity solutions through its modular Optimine information systems. These include 3D mine scanning, fleet administration, case management and equipment localization to optimize mine operation and use of equipment.
Connected tube solution
Digitalization is also benefitting the tube and pipe industry. Sandvik has developed an intelligent tube system featuring integrated sensors in the tube walls, sending signals to a cloud based system for online monitoring of the actual material behaviour of the tube inside the customers' processes. The system allows accessing the tube status and controlling critical parameters, such as pressure, vibrations and temperature. And more connected, intelligent products are in the pipeline.