Productivity – the value of digitalization
Although manufacturing is still in the early stages of transformation, the future of manufacturing is already here. This massive digitalization implies a huge potential for increased productivity, agility and improvements in work environments. At Sandvik, researchers are focusing on how the Internet of Things (IoT), Big Data and continued massive digitalization can help customers reduce costs, increase productivity and create new business opportunities.
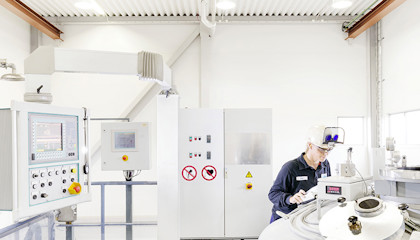
Industry 4.0 is the vision of manufacturing in the future. In this highly automated mode of production, sensors and IoT enable machines and products to "talk" and interact with one another and other relevant parts of the value chain, while providing continuous information to those monitoring the flow. It is possible to identify improvements in every part of the process.
Machines can predict failures and trigger maintenance processes autonomously, and self-organized logistics can react to unexpected changes in production. The potential for increased productivity, agility and improvements in work environments for humans, both in industrial production and mining, is huge.
"There are many challenges on the way, but the technology exists," says Ulf Hermansson, Strategical Technical Analyst at Sandvik Group Research and Development (R&D). "We are doing a lot of research and continuously releasing new products and solutions in this direction."
We've been working with automation, smart systems and other digital solutions for years, but now we are seeing accelerated development and new potential.
Ulf Hermansson
Sandvik has a long history of developing solutions for underground mining automation, which not only reduces the need for manual work, but also enables the finding of new sources of ore by mining in places where humans cannot safely go. Tuomo Pirinen, Research Manager at Sandvik Construction, says, "We help virtualize projects with software that enables customers to do detailed planning of how to proceed with drilling and blasting projects."
When the actual work starts, sensors and other sources align the information management system with exact data on rock conditions, effects of blasts, status of equipment and so on, allowing for immediate quality control, adjustments and optimization.
Riku Pulli, Vice President Mine Automation at Sandvik Mining, says sensors are now providing exponential amounts of data that pave the way for data-driven productivity improvements.
"Together with customers, we develop systems and algorithms to better understand and evolve the machines and the processes," he says. Development of IoT and increased understanding of Big Data signal a shift of business models in all kinds of industries, including mining. "In the future, companies can sell performance rather than just equipment," Pulli says. "We are definitely headed that way."
Vahid Kalhori, Manager Intelligent Machining at Sandvik Coromant, stresses that smart factories are more than just sensors, machine-to-machine (M2M ) connectivity and human interaction. "You need immediately accessible, available and reliable knowledge and knowhow in order to make quick and accurate decisions," Kalhori says.
Product Life Cycle Management, virtualization and other information systems and tools need to be developed to meet the higher demands of fast decision making. "Several of our recent solutions offered to the market answer to these needs," Kalhori says. For instance, Adveon™, an open virtual cutting tool library developed together with partners, paves the way for more simulation and testing in 3D environments, dramatically facilitating the development of cost-effective and innovative solutions.