Penny the robot - a custom-built solution
Predictable productivity is what Penny brings to Sandvik's insert manufacturing process.
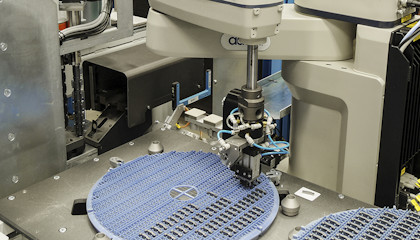
Penny works hard. She works all day, and never tire from the tedium of her job of moving carbide inserts from one side of a metal cage to the other.
Some might call her a robot, but Penny is far more than that. She's a custom-built material-handling solution, designed and built by the Sandvik Production Equipment team in Gimo, Sweden, under the direction of Project Manager Johan Eriksson.
"Penny is the first of her kind," Eriksson says. Once the final specifications were agreed to, she required more than a year to build. She has just recently been delivered to Sandvik's facility in Gimo, "the largest carbide insert factory in the world," where she is undergoing final acceptance testing.
She can 'see in 3D' what she is doing and is smart
enough to self-calibrate her movements
Johan Eriksson
Penny performs a critical step in the insert manufacturing process, placing up to 1,600 precision-ground inserts per hour onto racks for the PVD coating furnace, then sending the completed inserts off for marking and packaging.
Because Penny has an advanced vision system, she can "see in 3D" what she is doing and is smart enough to self-calibrate her movements. She is fast and accurate, but she also has a delicate grip – picking up onemillimeter-wide inserts is no problem for her, and there is never a risk of damaged or misplaced inserts.
Because of her predictable productivity, Sandvik can continue to offer high-quality products at a competitive price. "What we do here at Sandvik is a fine art," says an understandably proud Eriksson. "There's nothing else on the market quite like Penny."