Energy savings in the wake of a tsunami
Sandvik is providing technological solutions to Japanese companies seeking to reduce their energy consumption in response to the new reality of higher electricity prices since the Fukushima nuclear disaster.
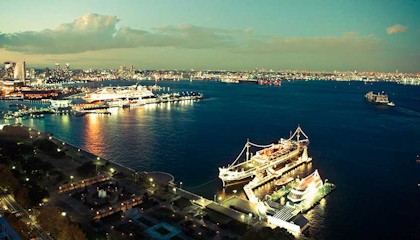
The tsunami that knocked out the Fukushima Daiichi nuclear power plant in Japan in 2011 permanently changed public attitudes towards nuclear energy. The country is still heavily dependent on some 50 reactors that provided around 30 percent of its electricity, but energy policy is moving Japan towards alternative sources. At present, 84 percent of Japan's energy comes from expensive imports, giving industry no choice but to seek less energy-intensive procedures.
The laws of material science fix the total amount of energy necessary to carry out a task. While there are no magic tools that eliminate power consumption, through process optimization we can reduce machine load and machining time to reduce the impact of expensive electricity.
"Japanese industry is generally energy-efficient, but more can be done," says Shinichi Takamiya, Product and Application Manager at Sandvik Coromant Japan.
The disaster at Fukushima triggered an array of initiatives to lower Japan's energy consumption and dependence on nuclear power. Sandvik responded by launching an energy-saving program aimed at reducing customers' energy consumption by 15 percent. The program promotes a variety of measures, including dry cutting, quickchange tool modular systems and lead-time reduction.
"Japanese customers, especially those with long production lines, have responded enthusiastically by joining the program," Takamiya says.
In a typical case, Sandvik helped a Japanese maker of airplane parts reduce energy consumption in machining. The solution involved replacing two machines with one multitasking machine equipped with our tools. This resulted in higher efficiency and time saved, while energy consumption fell by 43 percent.
Japanese companies have long adhered to continuous improvement programmes. In the past, energy was taken for granted, whereas today, reduction of energy consumption is a goal in itself, according to Takamiya.
Sandvik systematically documents the energy efficiency of its application methods and tools by collecting data. For example, CoroMill™ 490, a shoulder and face-milling cutter exercises low cutting forces and can reduce electricity consumption by 17 percent compared with an average reference cutter. CoroMill™ 490, featuring a combination of the tool and high-pressure coolant, decreases the time spent on managing chips. An operation machining 200 car parts per day, for example, can double production.
Sandvik initially promoted the program in the disaster-affected regions of Eastern Japan, but the market response since justified expansion to cover the whole country. "We are learning things that will benefit customers around the world," Takamiya says.