1969
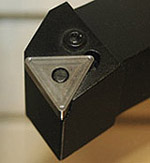
Sandvik is first in the world with surface-coated cemented-carbide inserts – Gamma Coating. New tools are produced for numerically controlled machines. The first cemented- carbide tools are sold to the Soviet Union. Steel-belt conveyors becomes a separate product area with head office in Fellbach, Germany. A subsidiary is set up in Singapore.
1968
The Group's annual sales exceed SEK 1 billion. The "Sandvik cutting data bank and data check" is introduced. T-Max tools for threading. Extension rods are fully carburized. Composite tubes for the pulp and paper industry. A regional warehouse is established in Singapore. A subsidiary in Thailand. Sandvik implements calculated depreciation in its annual reports.
1967
Arne Westerberg becomes managing director and Hugo Stenbeck is elected chairman of the board. The Sandvik Group is used as a concept for the first time in the annual report. The Parent Company now has 40 subsidiaries, of which 20 are production companies. Sales encompass 100 countries. In Mexico, production of cutting tools and rock tools is started. In Sydney, Australia, a plant is established for the production of rock tools. Companies are formed in Hong Kong and Venezuela. The word "steel" is removed from the names of the subsidiaries. A new clamping system for turning with negative inserts is produced: the T-Max P.
1966
Sandvikens Jernverk has become an international group. Net sales are allocated as follows: Europe 66% (of which, Sweden 18%), North and South America 23% and finally Africa, Asia and Australia 11%. U-bent stainless steel tubes with very long lengths are delivered to steam generators in the nuclear power industry. The company is invited to produce cladding tubes in Kennewick, WA, U.S., in partnership with an American producer of nuclear fuel. In Sweden, rock tools plants are under construction for button bits and extension rods. In Halesowen, UK, cutting tool production is in the process of being expanded. The plant in Fair Lawn, U.S., doubles in size. Rock tools production is started in Australia. Companies are founded in Turkey, Chile, Peru and Malaysia. A campaign is initiated in Sweden to recruit women for the purpose of reducing the existing labor shortage.
1965
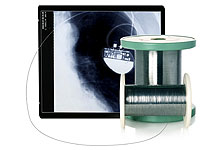
Conveyor belt production in Fellbach, Germany. Cemented-carbide plants are acquired in Germany. The ejector drill with brazed cemented-carbide inserts is an innovation in long-hole drilling. Subsidiaries are set up in Lisbon, Portugal, in Spreitenbach, Switzerland, in Manila, the Philippines, and in Wellington, New Zealand. Thin, stainless steel wire is developed for pacemakers.
1964
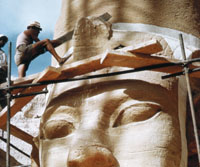
Specially designed Sandvik saws are utilized when stone sculptures from the Abu Simbel Temples in Egypt are moved in conjunction with the construction of the new Aswan dam at the beginning of the 1960s. The Group's employees now number over 12,000 following expansion outside Sweden. The first double-belt presses are delivered to the process industry. Subsidiaries are founded in Oslo, Norway, and in Ndola, Zambia.
1963
The share of exports regains pre First World War levels: 77%. The company develops cladding tubes made of zirconium alloys for the nuclear power industry and stainless razor blade steel. Low-carbon stainless steel is developed for the pulp and paper industry. Subsidiaries are founded in Barcelona, Spain, and in Vienna, Austria.
1962
A plant is opened in Brazil for both cutting tools and rock tools. The Group celebrates its centenary. The extrusion presses commence production in Sandviken and replace hot-rolling of tube. Coromantfabriken in Västberga has now been extended. Edge honing of cemented-carbide inserts is put into operation. Italian subsidiaries are merged in Milan. A subsidiary is founded in Warsaw, Poland.
1961
The Knux turning insert is introduced and becomes a top-seller for over thirty years. Jernverket invests in new sales subsidiaries of its own in countries like Mexico and Australia. A regional office is located in Japan. A large investment in research and development is marked by King Gustaf VI Adolf inaugurating a facility for steel research in Sandviken.
1960
The blast furnaces are closed. Big invest- ments are planned in Sandviken: Tube mill 60, Press mill 62, Tube mill 63, Pilger mill 64, Cold-rolling mills 61, 63 and 64, Electric arc furnace 64, Hardening plant 65 and Tube mill 68. Two extrusion presses are of substantial importance for seamless stainless steel tube. A new grade of stainless steel for spring wire is launched. The market for hacksaw blades grows sharply. The Indian company Sandvik Asia (shareholding 60%) is established and a plant is constructed. Production units also built in Mexico and Brazil.
1959
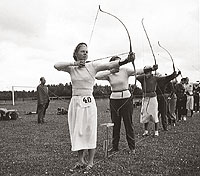
A larger new, electric arc furnace is installed. A strong management team is established in support of the newly elected managing director Wilhelm Haglund. "No more redundancies!" becomes the motto. Sandvik has a substantial lead in indexable inserts in Europe. The See plant in Sandviken that produces cold-drawn tubes and products manufactured from tubes, such as sports equipment, is acquired.
1958
The Göransson family's role as dominant owner is taken over by the Stenbeck family in conjunction with the new share issue. The T-Max technology with indexable cemented-carbide inserts and their tool holders, is introduced by Sandvik in Europe. The UK subsidiary moves to newly constructed offices and production facilities in Halesowen near Birmingham. Wilhelm Haglund new managing director.
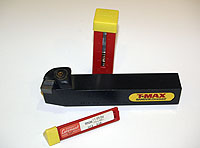
1957
Wilhelm Haglund becomes new vice president of production. A new share issue is completed.
The T-Max tool holder (picture) is presented in the U.S. Sandvik has developed a method of producing indexable inserts more cheaply than its competitors. Triumphal progress for Coromant cutting tools and for the manager Sven Wirfelt.
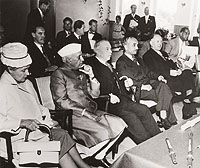
The Indian Prime Minister Nehru visits Sandvik in Stockholm, Sweden (picture). The German subsidiary moves to new premises in Düsseldorf. Production of rock tools starts in Brazil.
1956
Gimo concentrates on standard tools. The first computer is used in Sandviken. A machine is constructed for reaming tool holders for turning tools. Various special machines are designed for the production of cemented-carbide inserts.
1955
The Gammax turning tool, with a mechanically clamped insert, is developed and becomes a door-opener for tool sales. Tools start to be marketed by the major subsidiaries. The U.S. subsidiary moves to new offices and production plants at Fair Lawn, NJ, U.S.
1954
A new blooming mill is taken into operation in Sandviken. Rock tools account for all of the Group's profits when Steel, which accounts for 70% of sales, performs poorly.
1953
The cemented-carbide production plant Coromant-fabriken, in Västberga, Stockholm, Sweden, is completed. Production of cutting tools starts in Fair Lawn, NJ, U.S. The rock tools plant in South Africa wholly owned.
1950
Extension rods are developed for deep-hole drilling. The hot-rolling mill for strip steel and new works for tube production are taken into operation. Modernization of the production facilities in Sandviken initiated.
1949
A new company is set up in Germany. A subsidiary is founded in São Paulo, Brazil.
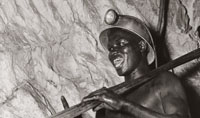
1948
A part-owned plant for the production of integral drill steels is established in South Africa. Erik W Forsberg becomes managing director.
1947
Production of Bessemer steel is closed in Sandviken. Long-term agreements regarding rock tools are finalized between Sandvikens Jernverk and Atlas Diesel. The concept "the Swedish method" makes its breakthrough in rock drilling. Own production of cemented carbide is initiated.
1946
Cutting tools are sold in Finland and Poland. Sales of rock tools expand considerably. Financial reasons force a post-ponement of portions of the post-war investment program.
1945
The Second World War ends. Exports' share of production increases to 37%. Iron ore from the company's mine in Bodås near Sandviken. Sales organizations in Germany and southern Europe destroyed by the war. Assab (Associated Swedish Steel AB) is founded with other steel companies for sales in distant countries.
1944
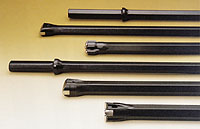
An investment program is prepared for the post-war years. Integral drill steels are utilized by customers.
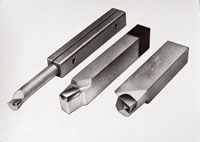
1943
The first cemented-carbide tools for metal cutting are manufactured. Subsidiaries in Italy and Finland start their local production. Sandviken becomes a town.
1942
The Coromant brand name is established following collaboration with KF's Luma-lampan. Cemented carbide-tipped integral drill steels are being developed.